A chemical cargo pump with 30 years of achievement
YOKOTA Enhanced Self-Priming Pump UPS type (PAT.)
Is it possible for a centrifugal pump to effectively suction chemical liquids?
Chemical tankers that can hold large amounts of various chemical liquids
have emerged as the most efficient and important means of delivering these
chemicals to Japan as it is surrounded by the sea in all directions.
Along with chemical tankers, a chemical cargo pump that is used for loading
and unloading chemical liquids has also been developed.
By the way, do you think that a chemical cargo pump must be a gear or screw
pump to effectively suction chemical liquids?
While it is, in fact, difficult to pump chemical liquids with a normal
centrifugal pump, the YOKOTA centrifugal-type Enhanced Self-Priming Pump,
in use since 1973, has gained a widespread reputation as an effective chemical
cargo pump.
How is the Enhanced Self-Priming Pump being utilized?
|
|
|
|
The Enhanced Self-Priming Pump-equipped chemical tanker
|
An Enhanced Self-Priming Pump located in the pump compartment (Main pump
in the front, Vacuum pump at the rear)
|
|
Why use the Enhanced Self-Priming Pump?
We will explain how the YOKOTA Enhanced Self-Priming Pump is utilized using
the examples of two tankers.
The tanker in the above-left photo (owned by marine firm H, 492 tons) was
constructed in 1991. It is a chemical tanker that mainly transports acetic
acid and is equipped with two Enhanced Self-Priming Pumps UPS type.
Pump specifications: 150mm bore diameter, 200m3 per hour discharge rate, 50m pump head capability, and interlocked with
a vacuum pump VP-S type.
The figure below is a layout drawing of the pump. It should be noted that
the pump compartment is located on the deck.
A gear pump can be used only from the bottom of the ship, and therefore
proves troublesome when cleaning the tank or pump due to its location.
With regards to safety, it is far more convenient to locate the pump on
the deck of chemical tankers that handle toxic and volatile liquids. The
Enhanced Self-Priming Pump can be installed on the deck with no problems
whatsoever. Of course, it could also be used at the ship bottom, allowing
the user to choose the best option.
|
Layout with the pump equipped on the deck
|
|
|
The tanker in the above-right photo (owned by marine firm D, 449 tons)
was constructed in 1992. It is a chemical tanker that mainly transports
acrylic acid and is equipped with three Enhanced Self-Priming Pumps UPS
type.
Pump specifications: 100mm bore diameter, 120m3 per hour discharge rate, 50m pump head capability, and interlocked with
a vacuum pump VP-S type.
For this ship, the pump compartment is located on the mid-deck.
Since acrylic acid is a highly toxic liquid and other liquids are also
often transported in place of acrylic acid, from an efficiency and safety
standpoint, the ship's captain and crewmembers are pleased to have the
pump located on the deck.
What are the advantages of using the Enhanced Self-Priming Pump?
Given the examples from above, it is clear that the YOKOTA Enhanced Self-Priming
Pump is a chemical cargo pump system that can substantially improve the
efficiency of loading and unloading work.

|
It can be installed on the deck.
|

|
It can substantially improve the efficiency of loading and unloading work.
|

|
It is safe.
|

|
Maintenance is easy and economical.
|
Enhanced Self-Priming Pump liquid suction structure (PAT.)
|
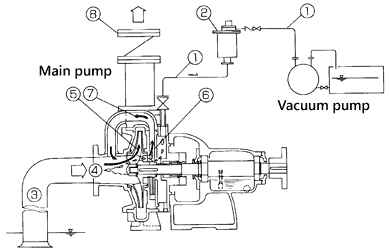
|

|
1:
|
Bleed pipe
|
|
2:
|
Float valve
|
|
3:
|
Suction pipe
|
|
4:
|
Pump suction inlet
|
|
5:
|
Main impeller
|
|
6:
|
Water-air separating impeller
|
|
7:
|
Return passage
|
|
8:
|
Non-Water Hammer Check Valve
|
|
|
The main pump is in the middle of the structural view, and at the above
right is the vacuum pump.
1.
|
The vacuum pump is activated.
|
2.
|
The cargo liquid is suctioned through the following passages according
to the degree of vacuum increase.
Suction pipe (3) -> Pump suction inlet (4) -> Main impeller (5) ->
Water-air separating impeller (6) -> Bleed pipe (1) -> Float valve
(2)
|
3.
|
When the liquid flows into the float valve (2), the buoyancy of the float
opens the air valve located above it.
|
4.
|
When air enters through the air valve, the liquid returns to the main pump
and is prevented from flowing into the vacuum pump.
|
5.
|
The main pump is activated.
|
6.
|
At this point, although there is air remaining in the suction pipe or main
pump, the liquid returns to the pump suction inlet (4) through the return
passage (7) due to the water-air separating action of the water-air separating
impeller (6), so that only air flows into the vacuum pump side.
|
7.
|
When the air in the main pump has been completely removed and operation
is stable, the vacuum pump stops. However, it reactivates when the sweeping
operation (stripping) starts.
|
8.
|
In the sweeping operation, some air is suctioned and mixed into the liquid,
but most of the air is concentrated at the center of the main impeller
(5).
|
9.
|
Since the accumulated air is exhausted by the vacuum pump through the holes
located in the main impeller (5) and water-air separating impeller (6),
the sweeping operation can be performed by continuous bleeding. As a result,
suction can be maintained until the bottom of the tank is visible.
|
|
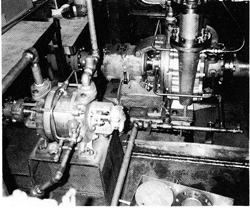
|
|
The Enhanced Self-Priming Pump in operation
(Main pump at the rear, Vacuum pump in the front)
|
Using the Enhanced Self-Priming Pump effectively
The following is a comparison of the Enhanced Self-Priming Pump and a common
gear pump.
|
Enhanced Self-Priming Pump
|
Gear pump
|
Installation
location
|
It is possible to install either on the deck or bottom of the ship.
It is advantageous to locate the pump on the deck when handling toxic liquids.
|
Equipped on the bottom of the ship.
|
Safety
|
Stable performance and a high degree of safety are ensured since the impeller
diameter and the rotation speed dictate the pressure inside the centrifugal
pump.
|
A safety valve is an absolute requirement because the pressure can rise
without limit, possibly causing a serious accident.
|
Discharge rate
adjustment
|
It can be adjusted freely using the valve.
|
The discharge rate is stable and cannot be adjusted.
|
Cost
|
The pump itself is expensive, but maintenance costs are low since the centrifugal
pump has fewer malfunctions.
|
The pump itself is inexpensive. Since the structure consists of gears that
contact each other to pump the liquid, the gears are considered as expendable
parts, and this results in large expenditures for replacement.
|
Pumped
liquids
|
Liquids with a specific gravity of 1.4 or less. For high viscosity liquids,
the possibility of cavitation must be considered.
|
Any liquid can be pumped.
|
The Enhanced Self-Priming Pump, of course, is not for general-purpose use.
It should be used properly by considering the above advantages and disadvantages.
1.
|
The strongest advantage of the Enhanced Self-Priming Pump is that it can
be located on the deck. When changing the pumped liquid, the pump or tank
needs to be cleaned, so if the pump is equipped on the deck, it is safe
and easy to perform the work when dealing with toxic liquids.
|
2.
|
Since the Enhanced Self-Priming Pump is a centrifugal pump, the impeller
diameter and rotation number dictate the pressure, so that stable performance
and a high degree of safety are ensured. However, since the pressure of
a gear pump rises without limit, the piping might be damaged if the safety
valve does not operate properly.
|
3.
|
The discharge rate of the Enhanced Self-Priming Pump can be adjusted with
the valve and this proves very useful when loading and unloading liquids.
However, the gear pump cannot be adjusted.
|
4.
|
In terms of cost, a centrifugal pump is slightly more expensive than a
gear pump, but in terms of maintenance, the centrifugal pump has fewer
malfunctions and only the packing or ball bearings, which are inexpensive
parts, require replacement. Therefore, it is a pump that can be used inexpensively.
The gears in a gear pump are expensive and easily damaged, and four of
them must be replaced at the same time when replacing the mechanical seal.
Therefore, the gear pump is expensive due to the amount of maintenance
required.
|
5.
|
In terms of pumping liquids, since the Enhanced Self-Priming Pump is a
bleed type, it can handle highly volatile liquids, but as long as the specific
gravity is 1.4 or less.
The gear pump can handle heavy or high viscosity liquids.
Therefore, it is important to decide whether to install a gear pump just
for handling heavy liquids a few times a year or to install a centrifugal
pump and handle light liquids only.
|
For details of this product, please refer to Enhanced Self-Priming Pump UPM, UPS types. |