Used in draining operation at Kanmon and Seikan Tunnels
YOKOTA pumps and valves
Undersea tunnels deliver us from island to island in no time.
Tunnels are convenient, but many types of equipment are under operation
day and night to maintain their function. One type of equipment is for
tunnel draining.
Tunnels, whether ground or undersea tunnels, are constructed across geologic
or water stratums, so ground water drainage is always necessary. For large
tunnels, the amount of drainage adds up to few thousand tons a day.
For ground tunnels, the down slopes toward the exit will do since water
flows downward for natural drainage, but this does not work for undersea
tunnels. Consequently, in addition to the tunnel shaft for the vehicle
road, drain tunnels and pump compartments are constructed to collect the
ground water, with drain pumps pumping it above ground immediately.
The requirements for a drain pump are as follows. Given the severe conditions
of these places alone, a pump that meets high tech standards is required.

|
Must have high pump head to pump water from deep underground to above ground.
|

|
No trouble with air suction during suction operation.
|

|
Has water hammer prevention.
|

|
Durability.
|

|
Hands-off automatic operation system equipped.
|

|
Easy maintenance inspection.
|

|
Must have high corrosion resistance especially for handling seawater.
|
Since the impetus for company formation in 1953 was "pump and valve
development for coal mining", we have created specialty pumps and
valves for various tunnels, and we now have been presented the opportunity
again with undersea tunnels. Thus, YOKOTA pumps and valves built with technical
expertise play an active, inconspicuous role behind the scenes.
|
The Kanmon Tunnel ... the YOKOTA Self-Priming Pump and Non-Water Hammer
Check Valve |
|
|
|
The Kanmon Tunnel is an undersea road connecting Honshu and Kyushu, which
began construction in 1939, and was completed in 1958.
Built for vehicle, bicycle and pedestrian traffic on National Route 2,
it has a total length of 3.5km, an undersea portion of 780m, with a maximum
depth from the sea surface of 56m.
Replacement work is periodically performed to prevent the Kanmon Tunnel
drain pumps and pipes from wearing out.
When completed in 1958, there were conventional type drain pumps equipped
in the drain pump compartments, but with the replacement work in 1973,
the YOKOTA Self-Priming Pump was adopted as a replacement.
In each pump compartment, pump operation is performed in shifts with a
few pumps as a precaution, furthermore, to guarantee safe drainage, each
pump is equipped with the YOKOTA Non-Water Hammer Check Valve and the built-in
No-Feed Detector.
Since then, the YOKOTA Self-Priming Pumps drain water in the tunnel day
and night, and have received high marks for their unique features and high
reliability to this very day.
From 1994 through 1995, the YOKOTA Self-Priming Pumps were renewed, at
which time the YOKOTA Seawater Resistant Stainless Steel Casting YST130N
material was adopted on the pump for higher durability and reduced maintenance
cost.
|
The YOKOTA Self-Priming Pump
and Non-Water Hammer Check Valve
under operation in Kanmon Tunnel
|
Why have the YOKOTA Self-Priming Pump and Non-Water Hammer Check Valve
been adopted?
The reason why the YOKOTA Self-Priming Pump has been adopted is because
of the following outstanding features in comparison to other conventional
self-priming pumps.

|
Superior suction force
|
Because of the patented suction (water-air separating) mechanism, the suction
force performance is superior. For general self-priming pumps, pumping
malfunctions are likely to occur at the foot valve, but the YOKOTA Self-Priming
Pump, with its high suction force, can perform pumping without a foot valve.
|

|
Air suction is no problem
|
Large amounts of air can be processed in the pump, and even if pumping
becomes subject to air suction or mixture of air during water pumping operation,
pumping operation continues by exhausting the air, and the pump returns
to normal pumping operation as soon as conditions are restored. Even continuous
suction of air-containing water (i.e., gas-liquid two-phase pumping) is
possible.
|

|
Low NPSH
|
Even if cavitation develops due to fluctuation in suction conditions such
as water level on the suction side, this pump can still continue pumping
operation and does not require allowance for NPSH. Stable performance is
also maintained under fluctuating suction conditions.
|

|
Intake piping across higher
elevations is possible
|
For general self-priming pumps, care must be taken not to create air accumulation
in the horizontal suction piping. Since the YOKOTA Self-Priming Pump pumps
water reliably even if there is air accumulation, there are no problems
even with suction piping shaped over high elevations.
|

|
Easy operation
|
Since there is no need for priming water operation other than filling the
casing with priming water during installation, handling is very easy. Maintenance
is also easy because of the simple structure.
|

|
Non-Water Hammer Check Valve
|
Unlike general check valves, the YOKOTA Non-Water Hammer Check Valve is
a patented check valve, which has been developed according to leading edge
hydraulic theory. The Non-Water Hammer Check Valve closes at exactly the
moment when change in flow from the normal to the reverse direction occurs,
that is, when the liquid in the pipes stops flowing after the pump is stopped.
As a result, water hammer due to reversed flow does not occur, thereby
preventing pipe ruptures and pump damage.
|

|
No-Feed Detector
|
The No-Feed Detector can be built-into the Non-Water Hammer Check Valve.
The switch operates according to valve movement from water flow to stop
the pump automatically when the flow rate is close to zero, preventing
dry operation of the pump. Therefore, automatic operation can be performed
with ease.
|
The following are model-based examples of the Self-Priming Pump used in
the Kanmon Tunnel.
Each pump has an original structure and features.
Actual use example 1 - Multistage Self-Priming Pump USM type
Six drain pumps of this type are used for suctioning seawater accumulated
at the bottom of a drain tunnel, pumping it to the ground surface located
65m above.
It is a reliable pump with a multi-stage, high pump head and patented self-priming
mechanism that enables outstanding self-priming performance.

|
Typical pump specification
|
|
Type:
|
USM-3-1510
|
|
Specification:
|
150mm x 3.3m3/min x 85m x 1750min-1 x 75kW
|

|
Auxiliary Non-Water Hammer Check Valve specification
|
|
Type:
|
SL-NBP-200
|
|
Specification:
|
Bore 200mm, JIS 10K, equipped with No-Feed Detector
|
|
|
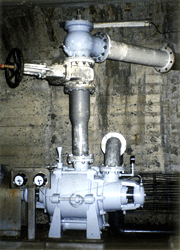 |
|
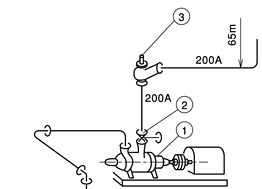 |
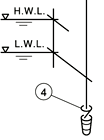 |
|
|
1:
|
Multistage Self-Priming Pump USM type |
2:
|
Discharge valve |
3:
|
Non-Water Hammer Check Valve (equipped with No-Feed Detector) |
4:
|
Foot valve (Not needed normally, but it is equipped here because of
the higher frequency of activation/deactivation at this location.) |
|
|
|
|
|
|
Multistage Self-Priming Pump
USM type
|
Non-Water Hammer Check Valve
SL-NBP type
|
No-Feed Detector
BP type
|
Self-priming mechanism of USM type:
The self-priming mechanism consists of a 1st-stage casing with a smaller
and larger passage forming a semi-double volute, and a 2nd-stage suction
casing with a 2nd-stage suction port.
|
1. Circulation flow
|
During self-priming, the water discharged from passage A in the semi-double
volute returns to the impeller after circulating in passage B-C, and is
discharged again into passage A.
|
2. Removal of bubbles
|
This recirculation flow mixes the water and the air in the center with
intense vortex D within the impeller and discharges it into passage A.
|
3. Water-air separation and exhaust
|
The water-air mixture is led from passage A to chamber B and separated.
The separated air is discharged via an exhaust valve. The separated water,
not entering the multistage side through the 2nd-stage suction port, returns
to the 1st-stage casing to repeat the self-priming operation until separation
and exhausting are completed.
|
|
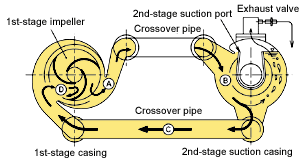
|
Actual use example 2 - Self-Priming Centrifugal Pump UHN, UHNM types
Eight pumps of these types are used for draining seawater as well as rainwater.
It is a reliable pump with a high pump head even though it is a single
stage pump. The patented self-priming mechanism also enables outstanding
self-priming performance.

|
Typical pump specification
|
|
Type:
|
UHN-2520
|
|
Specification:
|
250mm x 5.2m3/min x 21m x 1750min-1 x 37kW
|

|
Auxiliary Non-Water Hammer Check Valve specification
|
|
Type:
|
SL-SNP-250
|
|
Specification:
|
Bore 250mm, JIS 10K, equipped with No-Feed Detector
|
|
|

|
Typical pump specification
|
|
Type:
|
UHNM-0520
|
|
Specification:
|
65mm/50mm x 0.5m3/min x 85m x 3500min-1 x 15kW
|

|
Auxiliary Non-Water Hammer Check Valve specification
|
|
Type:
|
SL-NBP-80
|
|
Specification:
|
Bore 80mm, JIS 10K, equipped with No-Feed Detector
|
|
Self-Priming Centrifugal Pump UHN, UHNM types
|
|
|
Self-priming mechanism of UHN, UHNM types:
|
|
The pump casing consists of a smaller and larger passage forming a semi-double
volute and a cavity holder in the discharge nozzle.
|
1. Circulation flow
|
During self-priming, the water discharged from passage A in the semi-double
volute returns to the impeller through passage B-C, and is discharged again
into passage A.
|
2. Removal of bubbles
|
This recirculation flow mixes the water and the air in the center with
intense vortex D within the impeller and discharges it into passage A.
|
3. Water-air separation and exhaust
|
The water-air mixture is led from passage A to discharge nozzle B in a
cyclonic state and automatically separated by centrifugal force, and then
the water is recirculated through passage B-C. The separated air is then
held by cavity holder E, and compressed and discharged against the back
pressure.
|
|
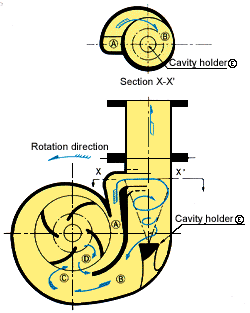 |
Actual use example 3 - Self-Priming Centrifugal Pump UHPR type with submersible
motor
Three drain pumps of this type are used for suctioning seawater, especially
where there is a possibility of submersion by seawater.
The pump body enables outstanding self-priming performance by the same
patented self-priming mechanism as described for the above UHN, UHNM types.
Moreover, the submergible motor is built into the pump and is completely
waterproof. YOKOTA Seawater Resistant Stainless Steel Casting YST130N has
been adopted for the pump material, so there are no problems with submersion
in seawater.
This highly reliable pump with its original mechanism and material has
been highly evaluated.

|
Typical pump specification
|
|
|
Type:
|
UHPR-1520
|
|
Specification:
|
150mm x 3.3m3/min x 20m x 1750min-1 x 15kW
|

|
Auxiliary Non-Water Hammer Check Valve specification
|
|
Type:
|
SL-NBP-150
|
|
Specification:
|
Bore 150mm, JIS 10K,
equipped with No-Feed Detector
|
|
|
|
The Seikan Tunnel ... the YOKOTA Non-Water Hammer Check Valve |
|
|
|
The world's longest undersea railway tunnel, the Seikan Tunnel connecting
Honshu and Hokkaido began construction in 1964, and was completed in 1987.
The tunnel is constructed not only for the conventional railway line but
also for the Shinkansen with a full length of 53.9km, an undersea portion
of 23.3km, and a maximum depth from the sea surface reaching to 240m.
The high-pressure pumps pump seawater penetrating the tunnel to above ground,
but the height to ground rises up to approx. 250m. Check valves have to
be used to prevent counter flow in case of emergency pump stoppage, but
if water hammer occurs on these check valves, an unexpected situation might
occur.
Therefore, the highly reliable YOKOTA Non-Water Hammer Check Valve has
been adopted for this important check valve. A total of twenty-one valves
were equipped in 1986, keeping the pump equipment safe.

|
Non-Water Hammer Check Valve specification 1
|
|
Type:
|
SL-SN-350
|
|
Specification:
|
Bore 350mm, JIS 20K and 30K
|

|
Non-Water Hammer Check Valve specification 2
|
|
Type:
|
SL-SNP-300
|
|
Specification:
|
Bore 300mm, JIS 20K and 30K,
equipped with No-Feed Detector
|
|
|
|
|
|
|
Non-Water Hammer Check Valve
SL-SNP type
|
No-Feed Detector
NP type
|
|
Why has the YOKOTA Non-Water Hammer Check Valve (PAT.) been chosen?
The reason for choosing the YOKOTA Non-Water Hammer Check Valve is because
of the following outstanding features compared to conventional check valves.

|
Due to the patented mechanism of the valve's quick response (open/close)
according to the water flow, there is no delay in valve closure and water
hammer does not occur.
|

|
Even with its large size, the single-disk, simple construction eliminates
breakdowns. Maintenance costs can be reduced considerably.
|

|
The No-Feed Detector can be equipped as safety equipment that prevents
dry operation of pumps.
|
Pressure change with time after pump operation is stopped |
|
YOKOTA Non-Water Hammer Check Valve |
Conventional check valve |
|
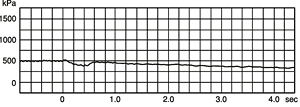 |
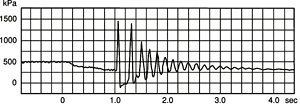 |
|
|
Regarding YOKOTA Seawater Resistant Stainless Steel YST130N
YST130N is a duplex type stainless steel alloy, which has been developed
originally by YOKOTA, and it has extraordinary seawater resistance.
Results of actual field tests clearly show that YST130N has excellent crevice
and pitting corrosion resistance.
|
Pitting corrosion resistance
|
Loss due to pitting corrosion
|
5% ferric chloride 40 deg C, 50 hours
|
|
Test piece after field test
|
YST130N
|
SUS329J1
|
SUS316
|

|
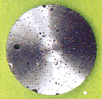
|
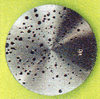
|
|
|
For details of each product, please refer to
Multistage Self-Priming Pump USM, UBM, MEF types
Self-Priming Centrifugal Pump UHN series (UHNM, UHPR types)
Non-Water Hammer Check Valve SL series
Seawater Resistant Stainless Steel YST130N |