|
|
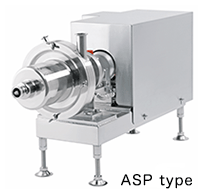 |
Patented in Japan, U.S.A., other
Bore
|
15-80mm(1S-2.5S)
|
Total head
|
0.1MPa
|
Capacity
|
0.01-0.15m3/min
|
>Selection & Dimensions |
|
|
This defoaming/degassing pump, with an interlocked vacuum pump, extracts
and discharges even dissolved gas in liquid with surprising efficiency.
Degasses liquid mechanically without using any chemical additive such as
hydrazine. Therefore it is safe, does not cause contamination, and greatly
reduces maintenance costs.
We also manufacture pumps that meet sanitary specifications.
Principle of degassing (PAT.) |
DP
type |
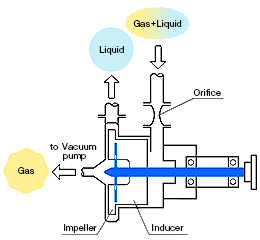 |
 |

|
When pumping liquid flows through the orifice into the intake part of the
pump, the dissolved gas in the liquid is separated from the liquid by decompression,
and the generated gas-liquid mixture is fed to the inducer.
|

|
The liquid in the gas-liquid mixture is pushed against the periphery and
stratified by rotation of the inducer, and the gas accumulates in the central
area of the casing at the same time.
|

|
The gas remaining in the liquid is further separated from the liquid, as
such liquid stratum is broadly exposed to high vacuum.
|

|
The gas is then drawn out by the vacuum pump through the impeller.
|

|
Any remaining liquid in the gas drawn out by the vacuum pump is separated
by the impeller, and returned to the intake side of the inducer.
|
|
|
ASP type |
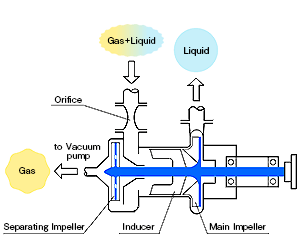 |
|
Defoaming/Degassing Pump ASP type |
|
|
Principle of Defoaming/Degassing Pump |
|
Surprising degassing efficiency! |
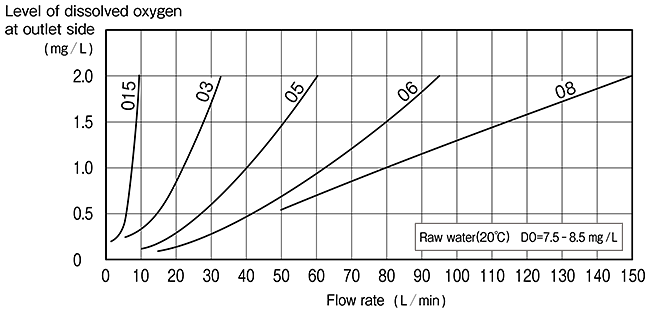 |
The above is a typical example of defoaming/degassing pump's degassing
performance.
Please contact us for more information. |
|
The outstanding degassing power is evident by the reduction of dissolved
oxygen from a near 8mg/L at the intake side (raw water at 20 degree C)
to 0.5mg/L or less at the outlet side.
|
Defoaming of thickener solution |
We are holding an "Online Exhibition" where you can experience
the same kind of tour as a real exhibition on the web.
Many videos showing actual examples of operation for processing various
liquids and evaluation methods for defoaming and degassing results are
available.
(> "Online Exhibition" page)
Continuous defoaming/degassing can be done easily and at low cost even
for food and beverage processing!
YOKOTA defoaming/degassing technology is high-profile new technology that
has been featured in news articles.
For details of the news articles, please refer to "Current Topics: Defoaming, Degassing".
Inquiries
|
:
|
Overseas team
|
Tel
|
:
|
+81 82-241-8672
|
|
|
|
|
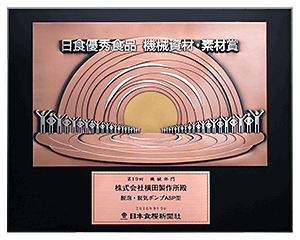 The "YOKOTA Defoaming/Degassing Pump ASP type" received the 19th
Nissyoku Excellent Food Machinery/Material Award in the machinery category.
The 19th Nissyoku Excellent Food Machinery/Material Award ceremony, established
by the Japan Food Journal Co. Ltd., was held September 9th, 2016 in the
Dai-ichi Hotel, Tokyo (Tokyo Minato Ward, Shinbashi) where the company's
Defoaming/Degassing Pump ASP Type received the award in the machinery category.
The Nissyoku Excellent Food Machinery/Material Award was established by
the Japan Food Journal Co. Ltd., in 1998, aimed at the development of machinery
and robots supporting the food industry and materials industry, and to
reward and show appreciation for their contributions, with this year being
the 19th time that the award was presented. The target products include
all machinery/robots, intermediate materials/sub-intermediate materials,
and the software utilized by them, which are useful to the quality improvement
of food products and support the food industry, such as food product-related
machinery/robots/apparatus and their software, intermediate materials/sub-intermediate
materials for packaging containers, food additives, essence, food ingredients,
and functional raw materials. The awards are decided by a selection committee
made up of representatives in various food industries and academics who
discuss with and consult each other in reaching decisions.
The company's "Defoaming/Degassing Pump ASP Type" enables the
instant and continuous removal of wasteful foam, bubbles and gas occurring
in the food product manufacturing process, and it has been credited with
contributing to the improvement of product quality and production efficiency,
which led to it winning the 19th Nissyoku Excellent Food Machinery/Material
Award in the machinery category.
Inquiries
|
:
|
Overseas team
|
Tel
|
:
|
+81 82-241-8672
|
|
|
|
|
|
|
Applications

|
Defoaming/degassing treatment of liquid foods and dairy products in each
production process such as boiling, immersion, extraction, oil extraction,
mixing, fermentation, and preservation; Defoaming treatment and transfer
of liquid products before bottling
<Application example>
Milk, soy milk, fruit juice, vegetable juice, vegetable paste, mustard,
egg mixture, gelatin, milk drink, ketchup, various juices, tea, fermented
liquid, yeast liquid, cream, jelly, vinegar, soy sauce, various seasonings,
other
|

|
Supply of degassed water for high quality (high transparency) ice making
|

|
Prevention of malfunction of various measuring instruments (flow meter,
density meter, other)
|

|
Defoaming/degassing and transfer of various raw material liquids
<Application example>
Various coating liquids, water-based paints, UV curable paints, urethane-based
paints, plating liquids, pigments, adhesives, chemical raw materials, grinding
oil, light oil, water-based polymers, insulating oil, desulfurization liquid,
rinse, detergent, gel, calcium carbonate, other
|
|
Outstanding performance is also demonstrated in applications such as extraction
from sealed tanks (vacuum tanks), and suction and transfer of liquid containing
large amounts of gas, foam and bubbles.
|
YOKOTA's proposal: Troubled with stubborn foam and bubbles ? ........ The
ASP type pump is the solution to the problem.
What if the ASP type pump, originally designed for degassing, is applied
to defoaming ?
As expected, the defoaming tests have proven excellent defoaming performance
as indicated below.
|
Examples of defoaming in the actual liquid (Click on the picture for enlargement. ) |
1. Soy milk |
2. Beverage concentrated liquid |
|
|
|
90 degree C, Specific gravity 1.02 (before
defoaming 0.6), Viscosity 30mPa-s |
 |
30 degree C, Specific gravity 1.22, Viscosity
500mPa-s, Air-content ratio 10% |
|
Improvement of production efficiency |
 |
Enhancement of yield rate |
|
|
3. Gelatin products |
4. Pickling liquid |
|
|
|
70 degree C, Specific gravity 1.28, Viscosity
2000mPa-s, Micro foam |
 |
6 degrees C, Specific gravity 1.1, Viscosity
80mPa-s |
|
Improvement of quality (commodification with
high transparency) |
 |
Improvement of quality |
|
|
5. Cream (food) |
6. Egg yolk |
|
|
|
50 degree C, Specific gravity 1.2, Viscosity
4000mPa-s, Micro foam |
 |
5 degree C, Specific gravity 1.0, Viscosity
7000mPa-s |
|
Improvement of quality |
 |
Improvement of quality |
|
|
7. Mekabu (thick seaweed leaves) |
8. Water-soluble paint |
|
|
|
15 degree C, Specific gravity 1.07 (before
defoaming 0.8) |
 |
Room temperature, Specific gravity 1.2,
Viscosity 30mPa-s |
|
Improvement of filling defect |
 |
Improvement of coating defects |
|
|
9. Water-soluble paint |
10. Solvent-based urethane paint (including MEK) |
|
|
|
Room temperature, Specific gravity 1.1,
Viscosity 400mPa-s |
 |
30 degree C, Specific gravity 1.1, Viscosity
3000mPa-s |
|
Recycling of recovered paint |
 |
Improvement of coating defects (Shortening
of defoaming time) |
|
|
11. Adhesive |
12. Glue |
|
|
|
20 degree C, Specific gravity 1.04, Viscosity
1100mPa-s |
 |
25 degree C, Specific gravity 1.2, Viscosity
10000mPa-s |
|
Improvement of coating defects |
 |
Improvement of coating defects |
|
|
13. Natural resin |
14. Facial cleansing gel |
|
|
|
75 degree C, Specific gravity 1.07,
Air-content ratio 15% |
 |
Room temperature, Specific gravity 1.0,
Viscosity 4000mPa-s |
|
Improvement of working efficiency
(filling defects) |
 |
Stabilization of filling amount |
|
|
15. Gel (pharmaceuticals) |
16. Grease |
|
|
|
30 degree C, Specific gravity 1.1, Viscosity
30000mPa-s |
 |
25 degree C, Specific gravity 0.9, Viscosity
unmeasurable |
|
Improvement of measurement precision |
 |
Improvement of quality defects |
|
|
|
|
The above is defoaming example by ASP type. Please contact us for more
information. |
Moreover, YOKOTA Degassing Equipment enables remarkable cost reduction
in the processing of various foaming liquids.
|

|
No clogging problems like that with membrane type equipment, no troublesome
maintenance required, and the pumps easily meet sanitary specifications.
|

|
Time required to eliminate foam and bubbles has been shortened, making
it unnecessary to install a large tank for stabilization of liquid.
|

|
The stirring operation of the built-in impeller simultaneously provides
favorable results such as liquid homogenization and reduced particle size.
|

|
With the self-priming and pressurized discharge capabilities, all processes
including suction, stirring, defoaming and transfer of liquid are achieved
in this single, compact pump, unlike conventional methods which require
installation of several components.
|
Use of YOKOTA Degassing Equipment greatly reduces costs of liquid processing.
|
Selection chart & Outer dimensions
DP type
Model No. |
Specifications (normal water) |
Base plate |
Motor |
Weight
(kg) |
Flow
rate
(L/min) |
Total
head
(MPa) |
Rotation
speed
(min-1) |
Bore
Suction/Discharge/VP |
A |
B |
C |
D |
E |
F |
G |
K |
L |
M |
N |
P |
P' |
S |
J |
Frame
No. |
Output
(kW) |
DP-0150 |
10 |
0.05 |
1800 |
Rc1 /Rc1/2 /Rc1/2 |
64 |
174 |
170 |
112 |
150 |
120 |
28 |
100 |
800 |
310 |
600 |
90 |
16 |
260 |
231 |
132S |
5.5 |
330 |
DP-0300 |
35 |
0.05 |
1800 |
25 /25 /25 |
86 |
220 |
170 |
118 |
185 |
160 |
28 |
100 |
800 |
310 |
600 |
90 |
16 |
260 |
278 |
132S |
5.5 |
340 |
DP-0500 |
60 |
0.05 |
1800 |
50 /40 /40 |
89 |
244 |
195 |
130 |
210 |
170 |
26 |
125 |
1050 |
310 |
800 |
120 |
19 |
315 |
174 |
132M |
7.5 |
390 |
DP-0600 |
90 |
0.05 |
1800 |
65 /50 /50 |
100 |
286 |
220 |
150 |
235 |
180 |
22 |
150 |
1250 |
360 |
950 |
120 |
19 |
340 |
208 |
160L |
15 |
570 |
DP-0800 |
150 |
0.05 |
1800 |
80 /65 /65 |
112 |
314 |
250 |
170 |
270 |
200 |
22 |
200 |
1350 |
400 |
950 |
150 |
25 |
400 |
260 |
180L |
30 |
1200
|
DP-S type (Sanitary specification)
Model No.
|
Specifications (normal water)
|
Base plate
|
Motor |
Weight
(kg) |
Flow
rate
(L/min)
|
Total
head
(MPa)
|
Rotation
speed
(min-1)
|
Bore
Suction/Discharge/VP
|
A
|
B
|
C
|
D
|
E
|
F
|
G
|
K
|
L
|
M
|
P
|
S
|
J
|
Frame
No.
|
Output
(kW) |
DP-0150S
|
10
|
0.05
|
1800
|
15A/15A/1S
|
71
|
181
|
170
|
112
|
150
|
140
|
28
|
80
|
850
|
300
|
256
|
426
|
138
|
132M
|
5.5 |
215
|
DP-0300S
|
35
|
0.05
|
1800
|
1S/1S/1S
|
71
|
205
|
170
|
118
|
165
|
145
|
28
|
80
|
850
|
300
|
256
|
426
|
163
|
132M
|
5.5 |
225
|
DP-0500S
|
60
|
0.05
|
1800
|
2S/1.5S/1.5S
|
77
|
232
|
195
|
130
|
180
|
145
|
26
|
80
|
1150
|
400
|
256
|
451
|
92
|
160L
|
15 |
260
|
DP-0600S |
90 |
0.05
|
1800
|
2.5S/2S/2S |
83
|
269
|
220
|
150
|
210
|
165
|
22
|
80
|
1200 |
400 |
256 |
476
|
88
|
160L |
15 |
380
|
DP-0800S |
150 |
0.05
|
1800
|
2.5S/2.5S/2.5S |
81
|
283
|
250
|
170
|
240
|
185
|
22
|
250
|
1450 |
550 |
225 |
475
|
48
|
200L |
37 |
780
|
The DP-0800S type is equipped with a channel base plate.
ASP type
Model No. |
Specifications (normal water) |
Base plate |
Motor |
Weight
(kg) |
Flow
rate
(L/min) |
Total
head
(MPa) |
Rotation
speed
(min-1) |
Bore
Suction/Discharge/VP |
A |
B |
C |
D |
E |
F |
G |
K |
L |
M |
N |
P |
P' |
S |
J |
Frame
No. |
Output
(kW) |
ASP-0115 |
10 |
0.05 |
2900 |
15 /15 /20 |
270 |
126.5 |
170 |
164 |
80 |
94 |
40 |
140 |
730 |
300 |
450 |
72 |
18 |
406 |
154 |
90L |
2.2 |
145 |
ASP-0310 |
35 |
0.1 |
2900 |
25 /25 /25 |
217.5 |
92.5 |
170 |
160 |
90 |
130 |
55 |
170 |
880 |
350 |
540 |
82 |
23 |
422 |
115 |
112M |
3.7 |
170 |
ASP-0510 |
60 |
0.1 |
2900 |
50 /40 /40 |
255 |
120 |
170 |
195 |
110 |
170 |
52.5 |
220 |
1130 |
525 |
690 |
112 |
30 |
477 |
50 |
132S |
7.5 |
230 |
ASP-0610 |
90 |
0.1 |
2900 |
65 /50 /50 |
298 |
139 |
195 |
225 |
125 |
185 |
60 |
275 |
1390 |
525 |
840 |
126 |
30 |
546 |
-39 |
160M |
15 |
400 |
ASP-S type (Sanitary specification)
Model No. |
Specifications (normal water) |
Base plate |
Motor |
Weight
(kg) |
Flow
rate
(L/min) |
Total
head
(MPa) |
Rotation
speed
(min-1) |
Bore
Suction/Discharge/VP |
A
|
B
|
C
|
D
|
E
|
F
|
G
|
K
|
L
|
M
|
P
|
S
|
J
|
Frame
No.
|
Output
(kW) |
ASP-0115S |
10 |
0.05 |
2900 |
15A/15A/1S |
245 |
101 |
170 |
135 |
80 |
75 |
40 |
80 |
700 |
230 |
236 |
541 |
269 |
90L |
2.2 |
165
|
ASP-0310S
|
35
|
0.1
|
2900
|
1S/1S/1S
|
245
|
120
|
170
|
160
|
95
|
110
|
55
|
80
|
800
|
300
|
257
|
587
|
285
|
112M
|
3.7 |
185
|
ASP-0510S
|
60 |
0.1
|
2900
|
2S/1.5S/1.5S |
278
|
143
|
170
|
190
|
110
|
115
|
52.5
|
80
|
617
|
321
|
132S |
7.5 |
190
|
ASP-0610S |
90 |
0.1 |
2900 |
2.5S/2S/2S |
319 |
160 |
195 |
225 |
125 |
145 |
60 |
180 |
1100 |
400 |
280 |
700 |
270 |
160M |
15 |
350 |
Note:
Specifications (flow rate, total head) and motor output power (kW) shown
above are based on normal water at 20 degree C, degassed to the level of
approx. 2mg/L. Such specifications and motor output power vary depending
on viscosity, specific gravity and required level of degassing of the actual
liquid handled. Please ask for details.
Specifications stated here may be subject to change without notice due
to product improvement.
|