The YOKOTA Mechanical Seal is a new type mechanical seal which requires
no external sealing water supply, being superior in corrosion resistance
and wear resistance, and is easily installed into pumps.
This mechanical seal has been adopted for pumps running under severe conditions
in industrial fields such as electric power plants, and has been rated
highly as an epoch-making mechanical seal.
This mechanical seal is also suitable for seawater and slurry liquid. |
>Selection & Dimensions |
|
Features
|

|
Stable seal performance for a variety of purposes because of the stationary
balance type structure.
|

|
Easy installation without remodeling a pump casing even when installing
to a pump that previously used gland packing.
|

|
Malfunctions due to adhesion of slurry, corrosion, or abrasion are not
possible because the pins and springs do not contact liquids.
|

|
Due to the self-alignment mechanism between its loose ring and rotary ring,
the sliding surface of the loose ring floats and efficiently follows the
sliding surface of the rotary ring.
|

|
Excellent wear resistance to high density slurry liquid because the SiC
of the sliding surface has excellent hardness, sliding performance, and
corrosion resistance.
|

|
YST130N is used for the parts that contact liquids. This is the duplex
type stainless steel YOKOTA has developed, and can be used for various
liquids because of its remarkable corrosion resistance, wear resistance,
and mechanical strength.
(For details of YST130N, please refer to this page.)
|

|
Supply of sealing water, such as industrial water, from the outside is
not required.
(Please use self-flushing method in order to prevent sliding parts from
possible dry-operation caused by a cavity generated within the stuffing
box due to generation of negative pressure in the case of self-priming
operation, or mixture of air in the case of force pumping operation.)
|
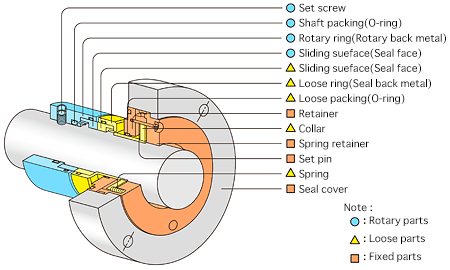
|
Performance
|
Condition of a self-priming limestone slurry pump in an electric power
plant after 6 months |
|
|
|
Pump in operation
|
|
Disassembled condition Lime-
stone slurry sticks to the
outside of mechanical seal. |
|
Disassembled condition
Limestone slurry sticks to the inside of stuffing box. |
|
As you can see, there are no problems despite slurry adhesion.
|

|
Pump specifications
|
|
1.5m3/min x 42m x 1750min-1
Liquid property: Limestone slurry 20wt%
Shaft diameter: 48mm
|

|
Running condition
|
|
Suction head: -4m
Running period: 6 consecutive months (including 21 stops and starts)
|

|
Measurement of abrasion on the seal surface
|
|
Seal surface
|
Amount of abrasion
|
Rotary ring
|
0.05mm or less
|
Loose ring
|
0.05mm or less
|
|
|
|
|
No abnormalities found in the pins and springs of the loose ring. |
|

|
Coarseness of the seal surface after operation
|
|
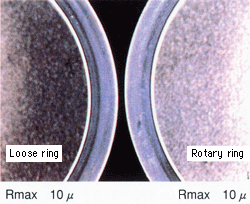
|
|
The conditions of the surface coarseness are very good.
|
|
Applications
|
The YOKOTA Mechanical Seal can be used for almost all kinds of liquid.
It proves excellent performance especially when used in pumps dealing with
the following liquids:
|
Electricity:
|
Smoke discharging desulfurizer, Seawater drawing, Waste water treatment,
other
|
Electronics:
|
Ultra-pure water production, Waste liquid treatment, other
|
Chemical:
|
Acid liquid, Alkaline liquid, Solvent, other
|
Sewage:
|
Polluted water, Sludge, Liquid containing earth and sand
|
Others:
|
Seawater, Condensed seawater, Liquid containing slurry, other
|
|
Selection chart & Outer dimensions
Application scope
|
|
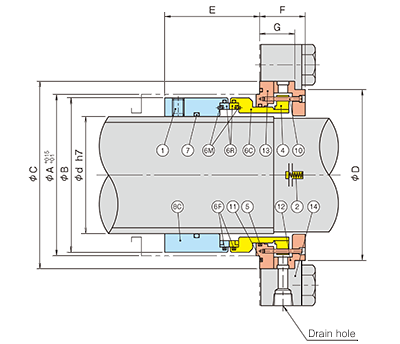 |
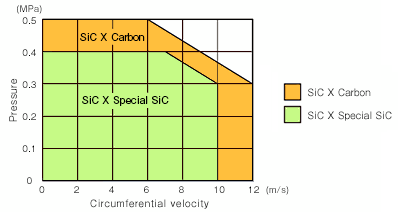 |
Part name
|
Q'ty
|
Material
|
1
|
Set screw
|
2
|
Hastelloy C
|
2
|
Spring
|
∗
|
Hastelloy C
|
3
|
Set pin
|
2
|
SUS316
|
4
|
Comp ring
|
1
|
SUS316
|
5
|
O-ring
|
1
|
Fluoric rubber
|
6R
|
Seal face
|
2
|
SiC
|
6C
|
Seal back metal
|
1
|
YST130N
|
6F
|
O-ring
|
2
|
Fluoric rubber
|
6M
|
Pin
|
2
|
Hastelloy C
|
7
|
O-ring
|
1
|
Fluoric rubber
|
8C
|
Rotary back metal
|
1
|
YST130N
|
10
|
Spring pin
|
2
|
Hastelloy C
|
11
|
O-ring
|
1
|
Fluoric rubber
|
12
|
Spring retainer
|
1
|
SUS316
|
13
|
Retainer
|
1
|
YST130N
|
14
|
Seal cover
|
1
|
SUS316
|
|
Dimensions
|
∗
Q'ty of springs
|
d
|
A
|
B
|
C
|
D
|
E
|
F
|
G
|
28
|
44
|
42.5
|
59
|
55
|
40
|
29
|
18
|
6
|
30
|
49
|
45.5
|
63
|
59
|
42
|
29
|
18
|
6
|
32
|
51
|
47.5
|
65
|
61
|
42
|
29
|
18
|
6
|
35
|
57
|
55
|
72
|
68
|
50
|
29
|
19
|
6
|
38
|
60
|
57
|
75
|
70
|
50
|
30
|
19
|
6
|
40
|
65
|
60
|
80
|
76
|
50
|
30
|
19
|
8
|
42
|
67
|
62
|
80
|
76
|
50
|
30
|
19
|
8
|
45
|
69
|
65
|
84
|
76
|
50
|
32
|
25
|
8
|
48
|
73
|
69
|
88
|
80
|
50
|
32
|
25
|
8
|
50
|
75
|
70
|
90
|
82
|
50
|
32
|
26
|
8
|
55
|
80
|
76
|
95
|
87
|
50
|
33
|
26
|
8
|
75
|
105
|
99
|
122
|
115
|
55
|
33
|
26
|
12
|
90
|
128
|
115
|
148
|
142
|
58
|
35
|
30
|
16
|
100
|
138
|
132
|
158
|
146
|
81
|
39
|
30
|
8
|
135
|
179
|
162
|
197
|
185
|
89
|
40
|
30
|
24
|
|
Note:

|
∗ is shown in the table of dimensions.
|

|
We can also manufacture seals with dimensions other than those listed above.
|

|
We can also manufacture cartridge type seals upon request.
|

|
The above combinations of materials are standard. We can also manufacture
these seals using other materials upon request.
|

|
Please use self-flushing method in order to prevent sliding parts from
possible dry-operation caused by a cavity generated within the stuffing
box due to generation of negative pressure in the case of self-priming
operation, or mixture of air in the case of force pumping operation.
|
Specifications stated here may be subject to change without notice due
to product improvement. |
|